In modern industrial production, drying technology plays a vital role in many fields. Spray drying and freeze drying are two common and widely used drying methods, but they have significant differences in principles, scope of application, advantages and disadvantages. This article will discuss in detail the basic principles, application fields, advantages and challenges of spray drying and freeze drying to help you choose the drying method that best suits your needs.
1. Basic principles of spray drying
Spray drying is a process in which liquid materials are atomized into tiny droplets by a sprayer and quickly dried by hot air. The process usually includes the following steps:
-
Material preparation: Make the liquid material to be dried into a uniform liquid or slurry.
-
Atomization: Atomize the liquid into tiny droplets through a nozzle or a centrifugal disk to increase its surface area.
-
Drying: Introduce the atomized droplets into a drying tower, contact with hot air, and quickly evaporate the water to form a dry powder.
-
Collection: Collect the dried powder product through a cyclone separator or a bag.
1.1 Application fields
Spray drying is widely used in pharmaceutical, food, chemical and other fields. Common applications include:
-
Pharmaceutical industry: production of drug powder, microcapsules, nanoparticles, etc.
-
Food industry: production of milk powder, coffee powder, protein powder, juice powder, etc.
-
Chemical industry: production of pigments, catalysts, detergents, etc.
1.2 Advantages
-
Quick drying: Spray drying can complete the drying process in a very short time and is suitable for heat-sensitive materials.
-
Uniform particle size: The particle size of the dried product is uniform and highly controllable, suitable for producing high-quality powders.
-
Continuous production: Spray drying can achieve continuous production and improve production efficiency.
1.3 Challenges
-
High energy consumption: Since a large amount of air needs to be heated, the energy consumption of spray drying is high.
-
Limited scope of application: Not suitable for materials with high viscosity or difficult to atomize.
-
Complex equipment maintenance: The nozzle is easily clogged and requires regular maintenance.
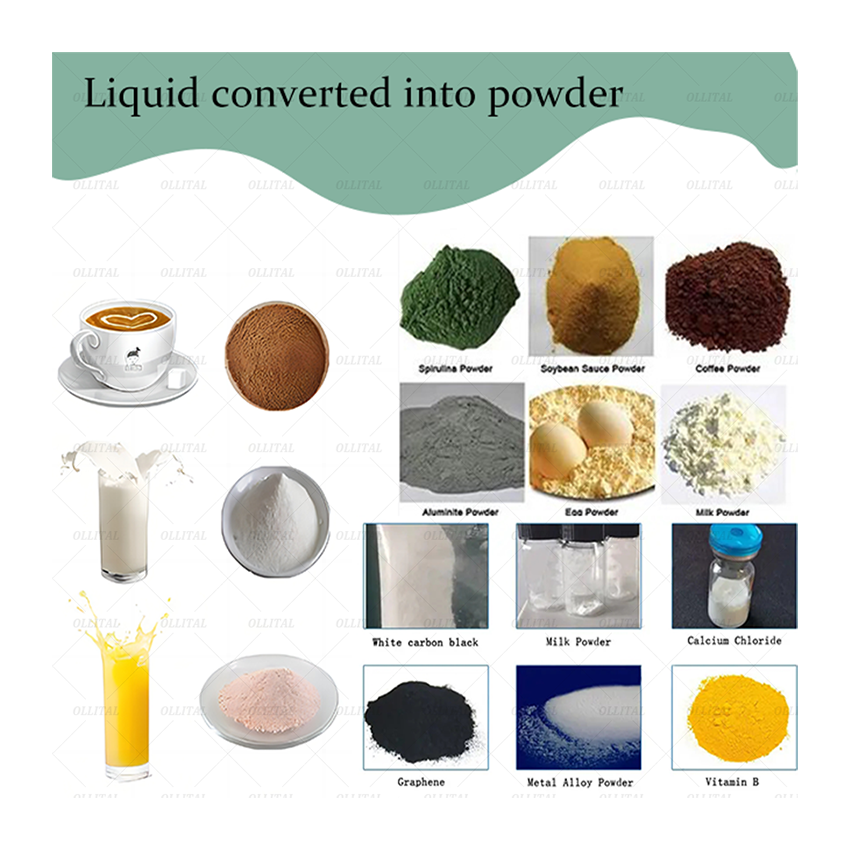
2. Basic principles of freeze drying
Freeze drying, also known as freeze drying, is a method of freezing water-containing materials at low temperatures and directly changing the water from solid to gas through sublimation in a vacuum environment to achieve drying. The process usually includes the following steps:
-
Pretreatment: Pre-treat the material to be dried into a suitable form (such as solution, suspension or paste).
-
Freezing: Rapidly cool the pre-treated material and freeze it into a solid state.
-
Preliminary drying: Remove the frozen water by sublimation in a vacuum environment.
-
Secondary drying: Continue to reduce the residual water in the material to achieve the final dry state.
2.1 Application areas
Freeze drying is widely used in pharmaceuticals, biological products, food and other fields. Common applications include:
-
Pharmaceutical industry: production of vaccines, antibiotics, protein drugs, etc.
-
Biological products: preservation of bacteria, enzymes, cells, etc.
-
Food industry: production of instant coffee, freeze-dried fruits, instant soups, etc.
2.2 Advantages
-
Maintaining biological activity: Freeze drying is carried out at low temperatures, which can effectively maintain biological activity and the original characteristics of the material.
-
High-quality products: The material structure is not easily damaged during the drying process, and the product has good rehydration.
-
Wide applicability: Suitable for drying heat-sensitive and high-value materials.
2.3 Challenges
-
High cost: Freeze-drying equipment is expensive, the operating cost is high, and it is suitable for high value-added products.
-
Long drying time: The freeze-drying process is long, and the production efficiency is lower than spray drying.
-
Complex equipment: The freeze-drying equipment has a complex structure and high maintenance requirements.
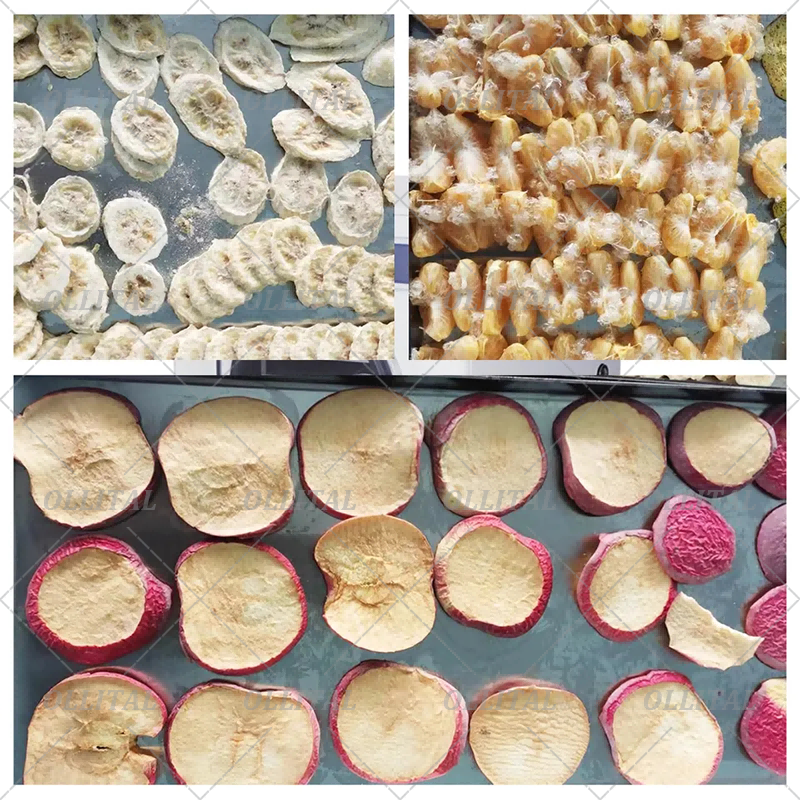
3. Comparison between spray drying and freeze drying
3.1 Applicable materials
-
Spray drying: Applicable to low-viscosity, easily atomized liquid materials, such as solutions, suspensions, etc. Not applicable to high-viscosity or solid materials.
-
Freeze drying: Applicable to materials in various forms, including solutions, suspensions, pastes and even solids, especially suitable for heat-sensitive and high-value materials.
3.2 Drying speed
-
Spray drying: Fast drying speed, suitable for occasions that require rapid drying.
-
Freeze drying: Slow drying speed, suitable for the production of high-quality products that are not in a hurry to dry.
3.3 Product quality
-
Spray drying: The product particle size is uniform, but it is easy to lose some active ingredients, suitable for general industrial products.
-
Freeze drying: High product quality, retaining biological activity and nutrients, suitable for high value-added products.
3.4 Energy consumption and cost
-
Spray drying: High energy consumption, but relatively low equipment cost, suitable for large-scale industrial production.
-
Freeze drying: High energy consumption and cost, suitable for drying high-value, heat-sensitive products.
4. How to choose the right drying method?
When choosing spray drying or freeze drying, the following factors need to be considered comprehensively:
4.1 Material properties
-
Thermosensitive materials: Choose freeze drying to maintain active and nutrient components.
-
Non-thermosensitive materials: Choose spray drying to improve drying speed and production efficiency.
4.2 Product requirements
-
High-quality products: Choose freeze drying to ensure high quality and rehydration of products.
-
General industrial products: Choose spray drying to reduce costs and improve efficiency.
4.3 Cost budget
-
High value-added products: You can choose freeze drying with higher costs to maintain product characteristics.
-
Low-cost products: Choose spray drying to save production costs.
4.4 Production scale
-
Large-scale production: Choose spray drying to achieve continuous and large-scale production.
-
Small-scale production: Choose freeze drying to meet high-quality, small-batch production needs.
5. Our Drying Equipment
When choosing drying equipment, it is crucial to choose the right supplier. Our company is committed to providing high-quality spray dryers and freeze dryers to meet the needs of different customers. The following are the main advantages of our equipment:
5.1 Company Profile
Our company has many years of experience in drying equipment manufacturing, focusing on the research and development and production of efficient and reliable drying equipment. Our equipment is widely used in pharmaceutical, food, chemical and other fields, and is deeply trusted by customers.
5.2 Advantages of Spray Dryer
-
Advanced Technology: Our spray dryer adopts the latest atomization technology and automatic control system to ensure efficient and stable drying process.
-
Efficient and Energy-saving: The equipment design is optimized to reduce energy consumption and improve production efficiency.
-
Diversified Choice: Provide a variety of specifications and configurations to meet different production scales and needs.
-
Perfect After-sales Service: Provide comprehensive technical support and after-sales service to ensure long-term and stable operation of the equipment.
5.3 Advantages of Freeze Dryer
-
Maintaining high quality: Our freeze dryer can dry under low temperature conditions to maximize the biological activity and nutritional content of the material.
-
Efficient and stable: The equipment is reasonably designed, easy to operate, and the drying process is stable and reliable.
-
Flexible customization: Provide customized solutions according to customer needs to meet the requirements of different materials and production scales.
-
High-quality materials: Use high-quality materials and advanced manufacturing processes to ensure that the equipment is durable and reliable.
5.4 One-stop solution
Our company not only provides high-quality spray dryers and freeze dryers, but also provides a full range of solutions, including equipment selection, installation and commissioning, operation training and maintenance. Our goal is to provide customers with one-stop services to help customers achieve efficient and stable production.
6. Summary
As two important drying technologies, spray drying and freeze drying each have their own unique advantages and application areas. Spray drying is suitable for non-heat-sensitive materials that need to be dried quickly, and has the advantages of high efficiency and continuous production. Freeze drying is suitable for high-value-added heat-sensitive materials, which can maintain biological activity and product quality. According to material characteristics, product requirements, cost budget and production scale, choose the drying method that best suits you to achieve the best production effect and economic benefits.
If you have more questions about spray drying or freeze drying or need further technical support, please feel free to contact us, we will serve you wholeheartedly.